Discover What is Porosity in Welding and Its Effect on Structural Stability
Discover What is Porosity in Welding and Its Effect on Structural Stability
Blog Article
The Science Behind Porosity: A Comprehensive Overview for Welders and Fabricators
Comprehending the elaborate devices behind porosity in welding is critical for welders and makers striving for flawless craftsmanship. From the make-up of the base materials to the complexities of the welding procedure itself, a wide range of variables conspire to either exacerbate or minimize the presence of porosity.
Comprehending Porosity in Welding
FIRST SENTENCE:
Assessment of porosity in welding discloses vital understandings into the honesty and high quality of the weld joint. Porosity, defined by the presence of tooth cavities or spaces within the weld steel, is a typical concern in welding procedures. These spaces, if not effectively dealt with, can compromise the structural integrity and mechanical residential properties of the weld, resulting in prospective failures in the completed item.

To spot and quantify porosity, non-destructive screening approaches such as ultrasonic testing or X-ray evaluation are commonly used. These strategies enable the recognition of internal issues without compromising the honesty of the weld. By examining the dimension, shape, and distribution of porosity within a weld, welders can make enlightened decisions to improve their welding procedures and attain sounder weld joints.
Aspects Affecting Porosity Formation
The incident of porosity in welding is influenced by a myriad of aspects, ranging from gas protecting efficiency to the ins and outs of welding criterion settings. Welding specifications, including voltage, existing, take a trip rate, and electrode kind, also effect porosity formation. The welding method utilized, such as gas metal arc welding (GMAW) or shielded steel arc welding (SMAW), can influence porosity development due to variations in warm distribution and gas coverage - What is Porosity.
Impacts of Porosity on Weld High Quality
The visibility of porosity likewise damages the weld's resistance to corrosion, as the caught air or gases within the gaps can react with the surrounding atmosphere, leading to degradation over time. Additionally, porosity can hinder the weld's capacity to endure pressure or impact, further endangering the overall high quality and reliability of the bonded structure. In important applications such as aerospace, auto, or architectural buildings, where security and sturdiness are critical, the detrimental results of porosity on Click This Link weld quality can have serious consequences, emphasizing the significance of reducing porosity via appropriate welding strategies and treatments.
Strategies to Reduce Porosity
Furthermore, making use of the suitable welding specifications, such as the proper voltage, current, and take a trip rate, is crucial in protecting against porosity. Keeping a constant arc size and angle during welding also helps lower the probability of porosity.

Utilizing the proper welding method, such as back-stepping or employing a weaving movement, can additionally aid disperse warmth evenly and reduce the possibilities of porosity development. By applying these methods, welders can successfully lessen porosity and produce top quality welded joints.
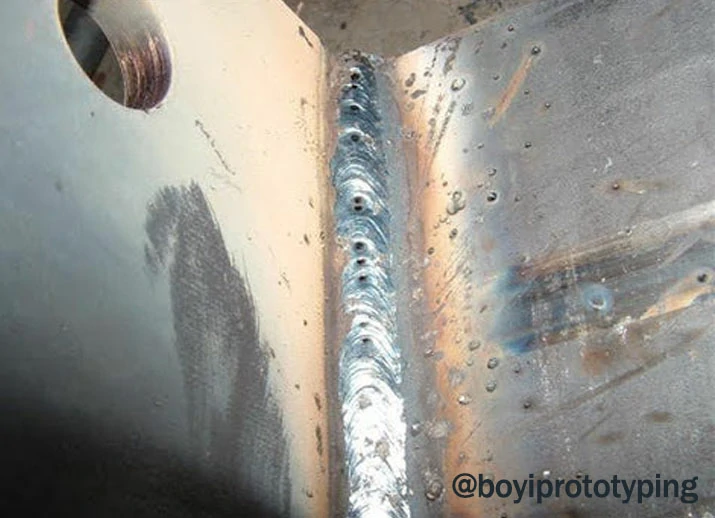
Advanced Solutions for Porosity Control
Applying sophisticated technologies and cutting-edge techniques plays a crucial duty in accomplishing remarkable control over porosity in welding procedures. One sophisticated option is the use of innovative gas blends. Shielding gases like helium or a mixture of argon and hydrogen can help in reducing porosity by providing much better arc security and boosted gas protection. Additionally, utilizing advanced welding techniques such as pulsed MIG welding or customized environment welding can also assist reduce porosity issues.
Another innovative option includes making use of sophisticated welding devices. As an example, making use of devices with integrated features like waveform control and innovative power resources can improve weld high quality and minimize porosity risks. Additionally, the execution of automated welding systems with specific control over criteria can substantially decrease porosity flaws.
Furthermore, including advanced surveillance and inspection discover this modern technologies such as real-time X-ray imaging or automated ultrasonic testing can assist in detecting porosity early in the welding procedure, enabling for instant restorative activities. Overall, incorporating these advanced services can significantly enhance porosity control and improve the total see quality of welded parts.
Verdict
In verdict, comprehending the scientific research behind porosity in welding is important for welders and fabricators to create high-grade welds - What is Porosity. Advanced services for porosity control can better improve the welding procedure and ensure a solid and reputable weld.
Report this page